How position sensors control a 60-ton CNC-stretch-bending machine
Fig. 1: CNC stretch-bending machine with Temposonics R-Series SSI.
There are applications where specially designed machines are needed to obtain the desired product. The company Günther Wensing GmbH has, for more than 50 years now, also specialized in the design of special machines in the field of CNC machines. These are used, among other things, in the railroad, aircraft construction and automotive sectors. In this article, Managing Director Jens Wensing explains how position sensors from Temposonics support the control of CNC stretch-bending machines, what requirements must be met and what role the position sensors play in Industry 4.0.
The special CNC machines from Günther Wensing GmbH offer users the possibility to automatically process metal in a wide variety of forms. These machining processes include stretching, punching as well as embossing, drilling, and calibrating the material. In some cases, all these machining steps are combined in one machine. “However, there are many customers who want only one machining step in the machine. This is especially requested when particularly large metal parts have to be machined,” Mr. Wensing begins the conversation. “We have been working with Temposonics for many years. In our special stretching machines, we use different position sensors to control the strokes of the cylinders in the systems that process the metal,” explains Mr. Wensing. “We only manufacture specialty machines, although there are also some standardized machines that are always designed on the same basis. However, we don’t integrate position sensors in these machines because we work with guide rails and recirculating ball bearing guides here.”
The position sensors from Temposonics are used in the special machines where it is not possible or advisable to use linear guide rails due to space constraints. Here, the sensors are then installed directly in the different cylinders of the plant, which then also protects the encoders from external influences and allows the company to use a very precise and reliable position measurement system for plant control.
3D stretching with 60 tons
One of the stretching machines that Mr. Wensing is very proud of is a special machine that can be used to produce aircraft parts and high-speed train components. “With this machine it is possible to stretch components up to 12 meters, which offers users a very wide range of parts. This is already an enormously large machine with a height of 4 meters, a width of 17 meters and, when folded, a depth of about 8 meters – there are not many of these in the world.”
A total of six Temposonics R-Series position sensors are used in this machine. “The cylinders with the integrated sensors are in the linear CNC axes, which are controlled via a CNC controller. Since we need a reasonable control behavior for the partially simultaneous movements, we need a very high resolution in the thousandths range so that the axes position afterwards with repeatability in the hundredths range.”
For this purpose, the displacement transducers from Temposonics were selected after careful supplier analysis, with production in Germany playing an important role here in addition to product quality and expertise. “This was already a decisive point for us, also regarding marketing and new customer acquisition. We wanted to work with a local supplier who, in addition to the desired products, also offers the appropriate service. And that’s how we ended up with Temposonics.”
To explain where and how the position sensors are used, one must take a close look at or inside one of the 2,500 mm long bending cylinders. The only opening is the exit for the cable that connects the otherwise completely protected sensor to the control system. “The cylinder and the displacement transducers must be robust to operate in harsh environments. You must remember that these machines are not built to be looked at, they are used and operated, and of course shocks and vibrations can occur. That is why it is advantageous to integrate the sensors and not to mount them externally. On this machine, we even went so far as to design the cylinder eyes on top of it to completely hide and protect the encoder. If we had worked with externally mounted linear guide rails, couplers, and rods, these would also be potential danger points. Just imagine the shock to the machine and the vibrations that would follow if something broke while stretching 60 tons. It’s an advantage to have as few external mechanics on the line as possible that could be damaged.”What properties must the sensor have?
In addition to the required robustness of the position sensors, it is important to Günther Wensing GmbH that one can still configure certain settings if necessary. For the operation of this special machine, position sensors of the R-Series with SSI output are required, because the protocol of Temposonics offers the possibility of internal linearization and in this way, one gets the highest accuracy for the machine. “Especially with strokes of up to two meters and a smooth and clean movement, which is in three dimensions, it is important that cylinders, mechanics, encoders and controls are all perfectly matched. Although the machine moves relatively slowly compared to others, the outer circumferential speed is already quite high due to the length, and with up to 60 tons, you are of course also moving a lot of weight. Then you need a reliable and precise distance measuring system, which we found with the Temposonics R-Series.”
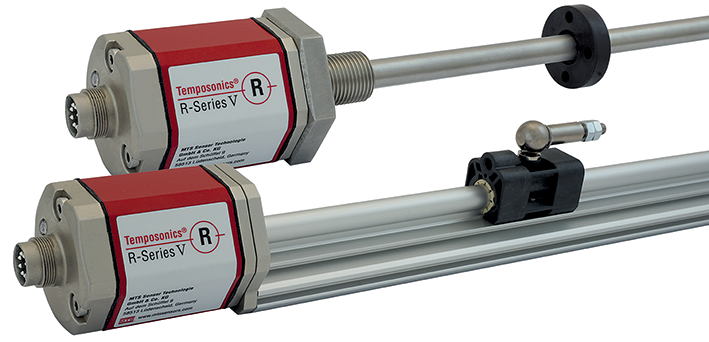
Fig. 2: Temposonics R-Series V with SSI output for Industry-4.0-capable applications.
Industry 4.0 for stretching machines
The arrival of Industry 4.0 does not stop at stretching machines. Predictive planning of maintenance and repair cycles, machine monitoring, and the general collection of data are elementary for the optimization of machines. However, not everything is yet possible in the way Mr. Wensing would like. “What limits us somewhat now is the fact that the controls do not yet allow us to connect the position sensors multiple times to further optimize our data collection. However, we are trying to get additional information about our globally distributed machines through other means. We use all hardware and software options to perform analyses and evaluate data to further optimize the applications for our customers, both those already in operation and those still under construction. The Temposonics position sensors play an important part in this. When we soon start using the new generation of position sensors, the R-Series V, we expect to get even more additional data from inside the plant due to the enhanced sensor characteristics. This would give us the opportunity, in combination with additional values from other sources, to optimize our machines even further to meet our customers’ needs.”
GET IN TOUCH WITH US
You have a question about one of our products or would like more details on a possible application?
Click here to fill in our request form
Don't want to miss out on the latest blog updates and other news?
Click here to subscribe to our newsletter
Total customer satisfaction
We live by the promise of unparalleled service that
enables us to take all available means to exceed your expectations.
Click here to find out how we support our customers